High Safety Bolt Connection
YONGYI MANUFACTURING
DIGITALIZATION X INTELLIGENCE
Yongyi took the lead in the digital and intelligent transformation of the workshop, the use of customised automation equipment, industrial software, Yongyi's core technology and intelligent manufacturing, to achieve the whole process of lean production of bolts, nuts, washers, high-quality fasteners production capacity of up to more than 60,000 tonnes per year.
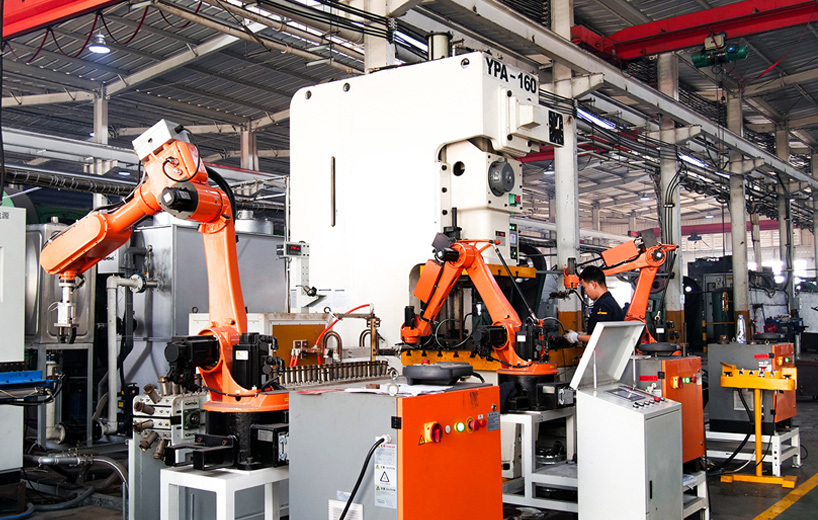
Hot heading automated production line
Self-developed advanced hot heading automatic line, adopting round coil heating, at the same time increasing the heating length, increasing the value of R-angle, controlling the heating temperature, the beginning of the calcination temperature, no water-cooling in the manufacturing process, avoiding the risk of forging failure in the moulding process.

Cold heading automated production line
At room temperature, it realises cold heading bolts and cold heading nuts to be formed at one time, with less loss of raw materials, high production efficiency, energy saving and environmental protection in the production process.

Hot zinc automated production line
The hot dip zinc production of all products is done independently, in strict accordance with the requirements of ISO10684 standard, digital control of the entire process of hot zinc, currently equipped with two hot zinc automatic line, automated production, improve the quality control of hot zinc.

Heat treatment automated production line
We have 6 continuous heat treatment mesh belt furnaces, which are strictly controlled in accordance with the requirements of CQI-9, so that the mechanical properties of the tempered products are uniform and stable.

Hobbing automated production line
Automatic loading and unloading, high production efficiency, stable output. Stable operation and accurate control precision.
YONGYI MANUFACTURING
INNOVATIVE TECHNOLOGY
Bolts, nuts and gaskets are produced in-house to achieve effective batch control, and at the same time to ensure the accuracy of the bolts, nuts and gaskets to improve the stability of the adaptability test of the connecting part.


Phosphate-free production
Improved the material lubrication process, to achieve the material conversion of non-phosphorus production, effectively avoiding the risk of phosphate generated by the fastener phosphorus brittle

No pickling process
The use of shot blasting process instead of the traditional pickling process, material treatment, surface treatment without acid washing, avoiding the risk of hydrogen embrittlement of the products brought about by acid washing.

Hot zinc nuts with one-time tapping
All hot zinc-coloured nuts are tapped once after hot zincing, which effectively improves the thread strength of the nut and avoids the nut stripping caused by the secondary threading.

Nut pre-coating process
Independent research and development of the coating line, while the use of advanced molybdenum disulfide pre-coating technology, coating of nuts, torque coefficient K control at 0.115-0.135, not only to achieve the adaptability of the test requirements, but also to achieve the gasket without pre-coating, to avoid the use of the process of rotation of the gasket caused by the problem of fastening failure.
Never-ending service
Looking forward to providing you with services
JIANGSU YONGYI FASTENER CO., LTD.
Address: Lianyungang, Jiangsu, China
Marketing Center
Address: Ningbo, Zhejiang, China
Tel:
+86-18006645721 (Domestic Business)
+86-15381932569 (International Business)
Email:
sales10@yongyifasteners.com (Domestic business)
sales@yongyifasteners.com (International Business)
Copyright©2024 Jiangsu Yongyi Fastener Co., Ltd. All Rights Reserved Powered by www.300.cn SEO Business License

Browse with phone